Yamaha Iwata, Japan plant tour: Where the magic happens
Yamaha gives us a rare look inside its manufacturing and design processes at its home base in Iwata.
Published On Oct 19, 2024 07:00:00 AM
9,696 Views
Follow us on
2024 marks 40 years of Yamaha’s operations in India, and the company marked this milestone by giving us a glimpse of how its bikes are made in Japan. Like most Japanese companies, Yamaha is very reserved with what they let the outside world see, which is why it was such a pleasant surprise that we got to see so much.
Problem-solving
Things began with a pre-factory visit presentation where we were told that the company was having difficulties in meeting varying demand for different models with the way its factory was geared to run. The existing manufacturing line setup was a batch system, and it was proving to be impossible to quickly adapt from manufacturing one model to the other, which resulted in wasteful downtimes when switching from model to model. The solution they came up with was elegantly unique, where the entire assembly line was replaced with automated guided vehicles (AGVs).
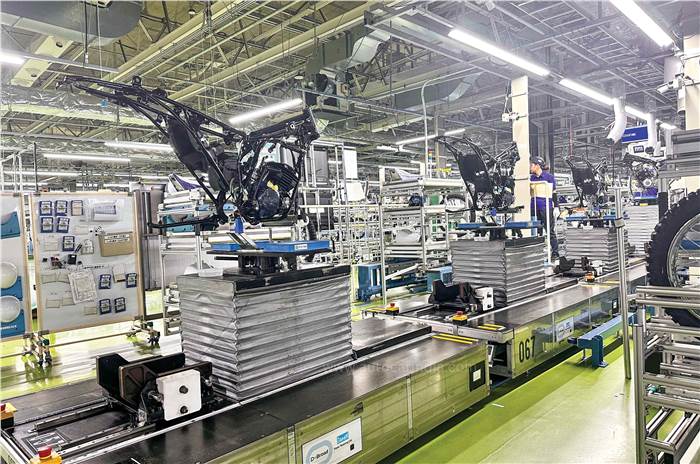
Each AGV now carries a motorcycle and moves along what would have been the line. The AGV can adjust its height based on the station it is at or even based on the height of the worker on that station. The tools on each AGV even automatically change their torque settings based on what bike is being assembled, which removes another area of potential human error from the equation.
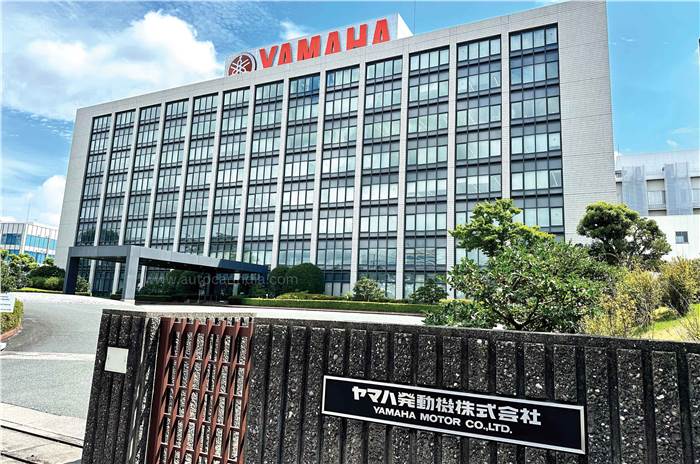
Some bikes take longer to assemble than others – for example, a 65cc dirt bike takes about half an hour, an R7 takes 70 minutes, and the FJR1300 takes the longest at two hours. To get around this, Yamaha created a system where the AGVs would skip some sections of the assembly line when it is carrying a simpler bike. If the AGV is carrying a motorcycle that will take longer to build, it will move to separate assembly line ‘cells’ where the work can be carried out. With all this innovation, Yamaha is able to build 40 different models at this factory, and it can still seamlessly move from model to model with minimal delays.
Fire and fury
After marvelling at a bunch of AGVs silently carrying motorcycles in different states of assembly through the factory, we then got to visit the company’s aluminium foundry. Yamaha is quite unique in the motorcycling world in that it casts its own aluminium parts, including the chassis and the wheels.
What we got to see was Yamaha’s unique wheel-forging process, which is another one of the company’s innovations. Instead of making a fully forged alloy wheel, which is both time-consuming and more expensive, Yamaha first casts the wheels in a conventional process and then forges just the rims. This happens in a spectacularly fiery process that they call spin-forging.
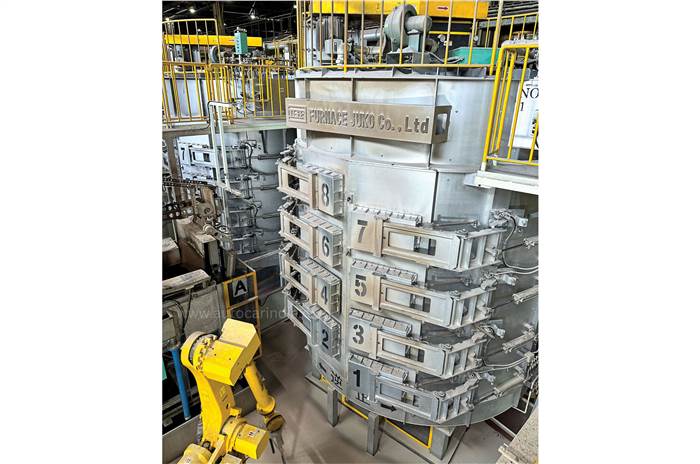
Once the wheels are spin-forged, they undergo two separate heat treatments in huge vertical ovens with individual compartments for each wheel. Each of these gigantic ovens has 112 compartments, and one wheel comes out every two minutes. Yamaha says it makes about 700-800 wheels like this every day. The result of all these efforts is a wheel that’s lighter than a regular cast one, but it’s so cost-effective that it can be installed on even the base 900cc models.
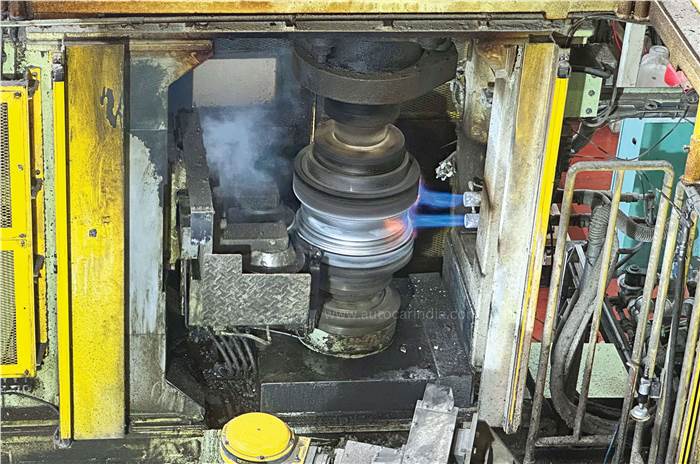
While we didn’t get to see the chassis and swingarm casting sections of the foundry, we were told that Yamaha does both die-casting and gravity casting. The former is a more affordable process, and bikes like the MT-09 use die-cast aluminium frames, which are cast in just two pieces that are bolted together without welds. Gravity-cast frames are used exclusively on supersport bikes like the R6 and R1. In total, the Yamaha foundry uses about 50 tonnes of aluminium per day.
The creative process
The insight into Yamaha’s motorcycle-making process ended with a fascinating chat with Hirotoshi Noguchi, who is the general manager of the Product Design division at Yamaha’s Creative Centre. Hiro san talked to us about a number of things, including the fact that designing small sportbikes like the R15 for India can be even more challenging than designing full-sized superbikes. Costs are crucial with smaller bikes, riding positions are less extreme, and the seat needs to come down while the handlebars need to go up. Turning radiuses also have to be tighter, and he explained that all of this makes designing a good-looking small sportbike all the more difficult.
When the topic moved to aero in MotoGP, he didn’t shy from expressing his personal dislike for oversized wings on motorcycles. But he also admitted that there has to be a balance between beauty and function. “I don’t think wings are beautiful, but if I were an engineer, I might think those wings are beautiful. As a designer, I have to think about who I am building for. If a new R series sportbike would look more beautiful with wings, I would put wings on that bike.” And sure enough, a couple of weeks after our chat, Yamaha revealed the updated US-spec R1, which looks mean despite the fact that it now has wings!
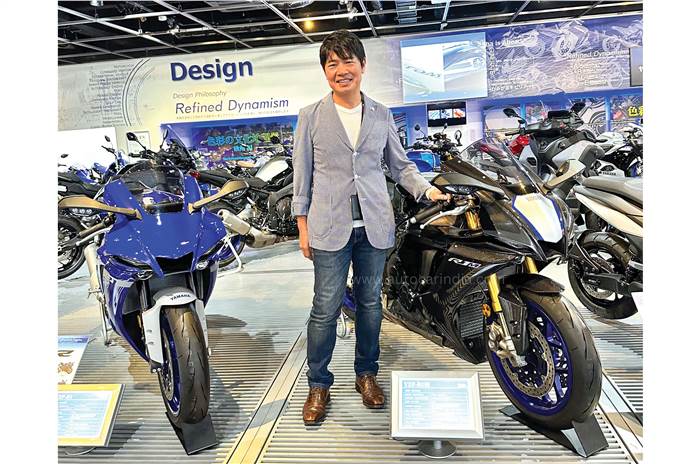
Hiro san ended the talk on an optimistic note when it comes to the future of motorcycle design because he believes you can do things with EVs that just aren’t possible with internal combustion motorcycles.
Yamaha motor communication plaza museum
We also got to peek into Yamaha’s rich, nearly 70-year-old heritage with a visit to the museum at the company’s communication plaza. The fascinating thing here was to see how much more the company has been involved in, apart from just motorcycles. In today’s world, Yamaha’s boats and jet skis are well known, but there are so many more unexpected things you’ll see at the museum, including trikes, lawnmowers, snowmobiles, and more.
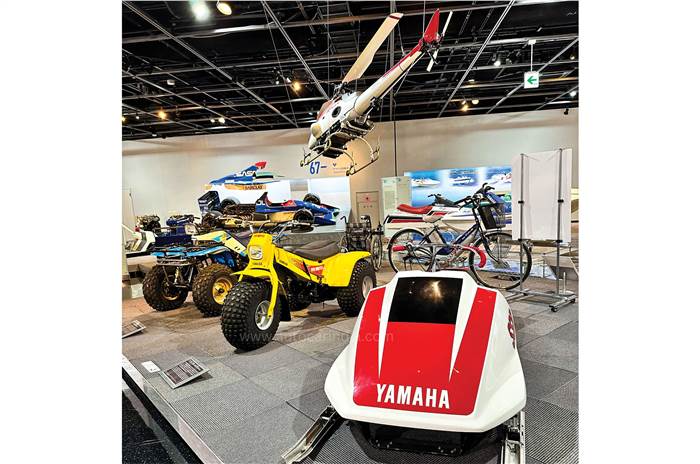
Some may also be surprised to see a few cars parked there, including a Lexus LFA and even an old Jordan F1 car from the early 1990s.
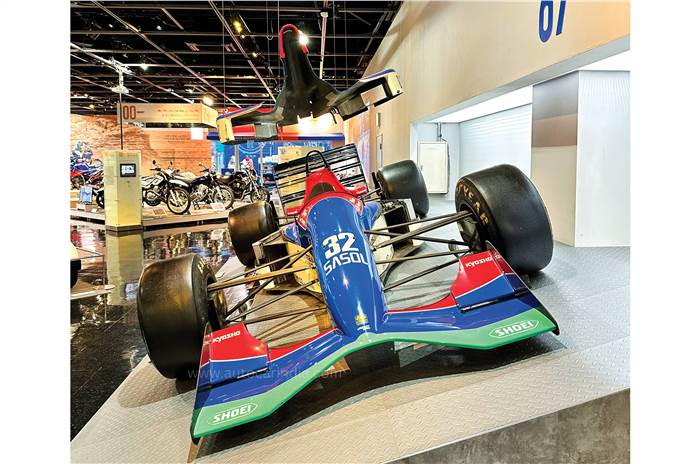
The cars were there because Yamaha either helped assist with the engine tuning (LFA) or built the engine outright, as was the case with the 3.5-litre V12 in the F1 car.
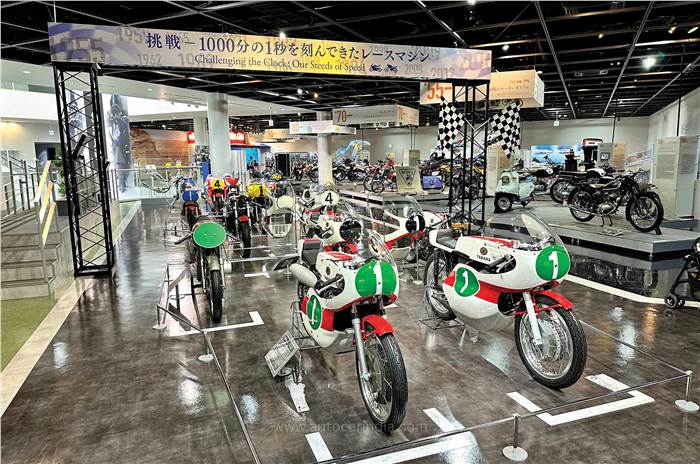
But beyond the oddities, the Yamaha museum is a goldmine for a racing enthusiast, with multiple race bikes, which were once ridden to victory by iconic names, including Rossi, Roberts, Lawson, and so many others.
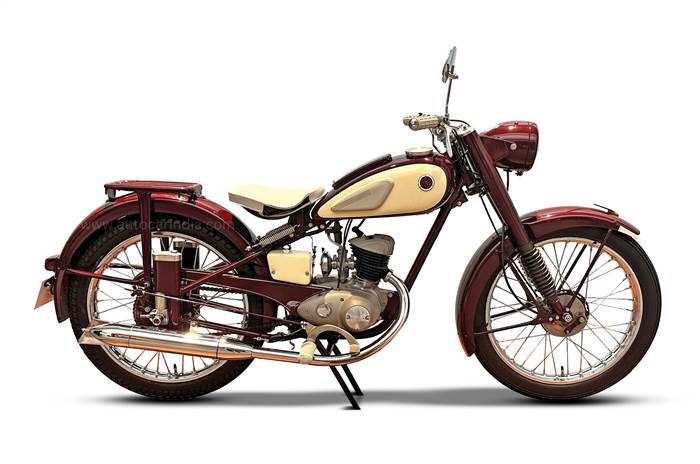
You’ll also get to marvel at some of the earliest Yamaha bikes, including the YA-1, which was the bike that started it all. Fun story: It turns out that Yamaha has been a premium brand from day one because the 1955 YA-1 was priced over 10 times the average starting salary of a Japanese college student in that era.
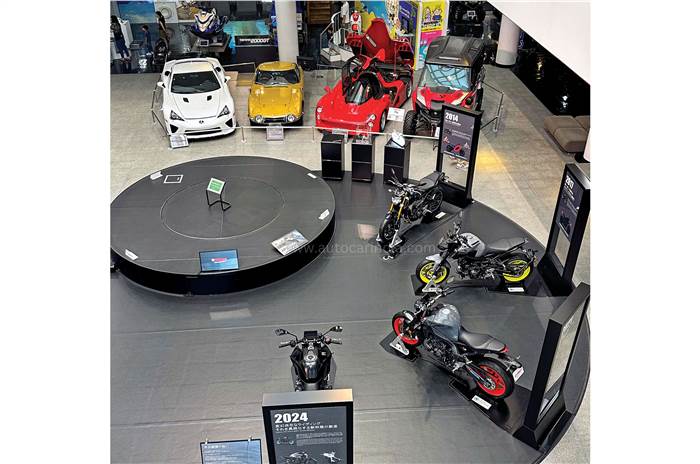
However, the company still managed to sell 11,000 of them in three years, which is a nice reminder that people are always willing to pay extra for the good things.
Also See: Yamaha MT-09 review: Standard, SP, Y-AMT ridden
Hero Karizma XMR vs Yamaha R15 V4 comparison review: Dream catchers
Copyright (c) Autocar India. All rights reserved.
Comments
Member Login
Personal Details
No comments yet. Be the first to comment.