In the very early days of Formula One, the only data a team and driver had came from a stopwatch. Today, while the tick-tick-tick of the second hand is still the ultimate measure of who’s fast and who’s not, it is only the tip of an iceberg of data that tells Formula One teams how quick their car is and why.
“Once upon a time the only data was what you got from the stopwatch, the lap time, and the feedback you got from the driver,” the Renault F1 Team’s head of vehicle performance Chris Dyer told Autocar India in an interview. “At the very beginning that was the limits of the data. As time has progressed and technology has progressed, the amount of data we get has grown exponentially. Obviously the stopwatch and the driver are still important sources of data but the amount of data has just grown exponentially.”
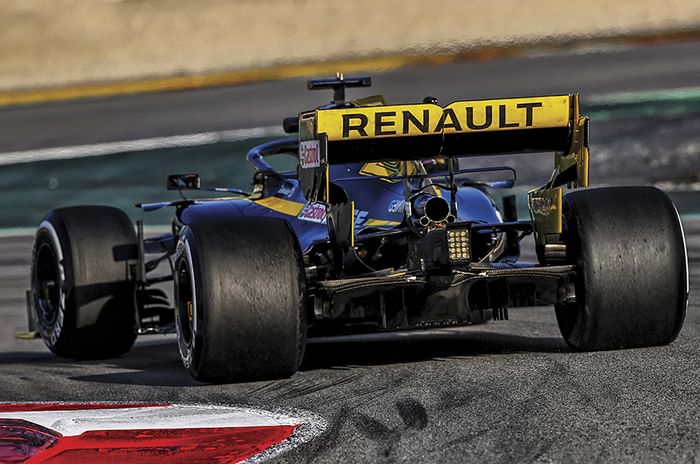
Data is the currency, if you will, that buys performance. It is a key part, probably the most key part, of the performance puzzle.
“I think Formula One nowadays is absolutely 100 percent dependent on data at all levels,” said Chris Dyer. “Everything we do now is data-driven, every decision we take is data-driven. It’s absolutely critical to every performance decision that’s made.”
“Obviously data in itself is not a direct driver of performance,” he went on to say. “Data in itself will not make the car go faster. It’s what we do with that data that is important.”
Effectively, what Chris Dyer is saying is that the more you know about the way your car works, the more insight you will have into its strengths and weaknesses. The data is that knowledge that tells teams not just whether their car is fast or slow, but more crucially – why.
Today, there is almost nothing teams don’t know about their cars. Daniel Ricciardo and Nico Hülkenberg’s respective Renault R.S.19s each generate hundreds of gigabytes of data over a single Grand Prix weekend. Everything is measured in real time – the way the air flows over the car; engine, brake and exhaust temperatures; the loads placed on the car’s tyres or bodywork because of the different forces a car goes through; nothing – not even a stray gust of wind, a millimetre of steering correction, a brush of the brakes, a feathering of the throttle – goes unnoticed. There is no blind spot.
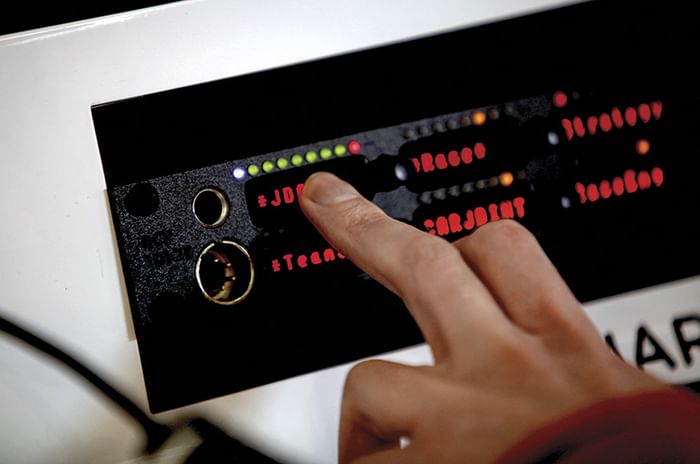
Different parameters are measured at different intervals. For example, Renault may log 1,000 samples of data per second during a single gear shift. Other, less critical, information may only be measured once every second.
Sometimes the data will pick up something a driver is doing even though he may not be aware he’s doing it. “You’re resting your foot too heavily on the brake pedal down the straights,” an engineer may inform a driver over the team radio, making him aware that he is inadvertently applying a minuscule degree of brake pressure that’s costing him straight-line speed. “You’re pressing ‘radio’ instead of ‘energy’,” a driver, accidentally pressing the radio button instead of the energy button on his steering wheel, was told at the recent Chinese Grand Prix.
All of this data is gathered by over 200 sensors fitted to each car and is streamed back in real time to the pit garage and to the team’s factories in Enstone and Viry, across more than 1,000 channels. “As soon as the data is back in the garage, in the pit lane, we start treating it,” said Renault’s Chief Information Officer Pierre d’Imbleval. “So we have a proper data centre in the garage, running approximately 160 virtual machines, virtual servers, with many algorithms to enrich the raw data that we get out of the car.
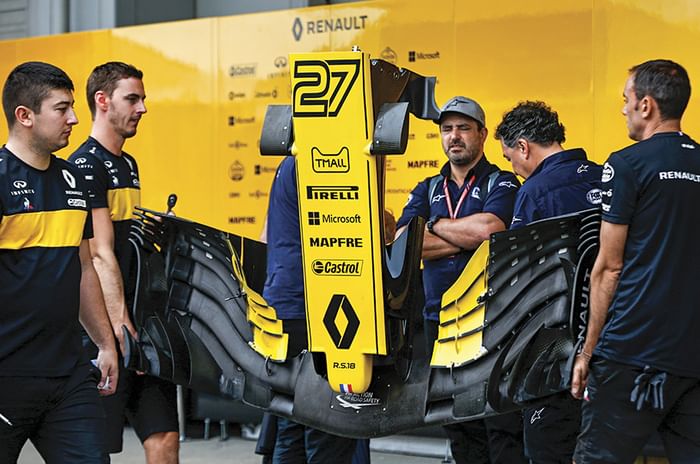
“After that we have connectivity from the garage to the factory. So we have a large-bandwidth link provided by a network operator to be able to send all that data back to the factories to make even further analysis with more computing power that we have in the factories – both in Enstone and in Viry.”
“If something goes wrong in the garage, we can actually do the analysis in the factory and send the results back to our engineers on the track. And the opposite is true – if we lose connectivity with the factory, there is enough computing power at the track to run the main results that are necessary.”
It is impossible to physically sift through all of the data generated, which can easily run into terabytes when data from simulations, the wind tunnel and test benches is added to the hundreds of gigabytes the cars alone are logging every race weekend. It needs to be made relevant and cut down to digestible sizes that engineers can then process.
“Formula One has been gathering quite a large amount of data for many years,” said John McColgan, Renault’s head of control systems. “Our ability to log that quickly and the quantity of data that we can log have increased quite considerably in the last 15 years. I think the challenge that we face now is not so much the acquisition of information on the car. The challenge really is to make sense (of it).”
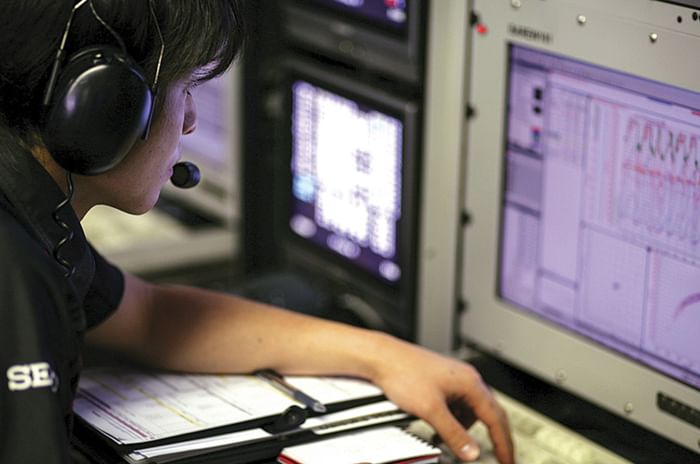
The Renault F1 Team uses a number of tools, machine learning and artificial intelligence to not only convert data into easily understandable graphs and charts but also to flag engineers’ attention to anomalies, which could indicate a looming problem in sets of data they would not otherwise look at.
“This is a great area of development for us, to bring more artificial intelligence into the way we look at our data,” said Pierre d’Imbleval. “We want to focus on what goes wrong during an event. But also we would like to be able, with machine-learning algorithms, to detect unexpected patterns in our data measurement. So that’s something we start looking at now. It is the early stage of that domain but quite promising in terms of making sure that we won’t miss anything from what happened on the track.”
Of course, the point of collecting all of this data is to unlock more performance and the different ways in which this performance is unlocked are wide-ranging. It could be an instruction to the driver to change the differential settings on his steering wheel, which could make the car go faster through a corner. It could mean adapting race strategy to account for a sudden safety car. But these are all ways in which teams can hone the underlying performance that exists in the car.
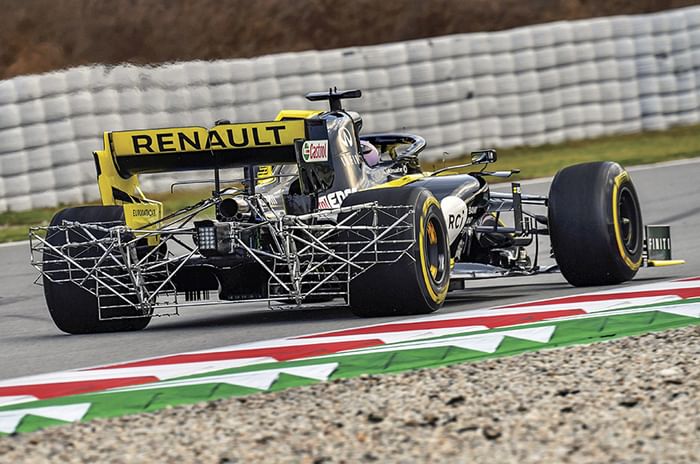
On a much larger level, it is the gathered data that determines that underlying potential in the first place. Computational Fluid Dynamics (CFD), once only a complement to wind-tunnel testing, is increasingly beginning to lead the design and development process. The quality of data and the engineers’ interpretation of that data that is presented to the CFD software in the form of inputs determines whether the car on track behaves the way simulations predict it will. This is known as correlation and can make the difference between teams coming up with a winning design or ending up with a back-of-the-grid car.
“There are quite a number of factors that do affect correlation,” said Paul Cusdin, Renault’s head of CFD. “An awful lot of them are just local operating conditions. So for example, the temperature on the day, the gusts of wind, deflections of the geometry, whether we’ve got the front wing in particular deflecting in the right way as to how it would be on track, the tyre shape…”
These are all fed into the CFD software as data. If they’re not accounted for accurately, the simulations that a team’s entire car design is based on go awry, which means the actual car’s behaviour on track will be way off from what the team expects.
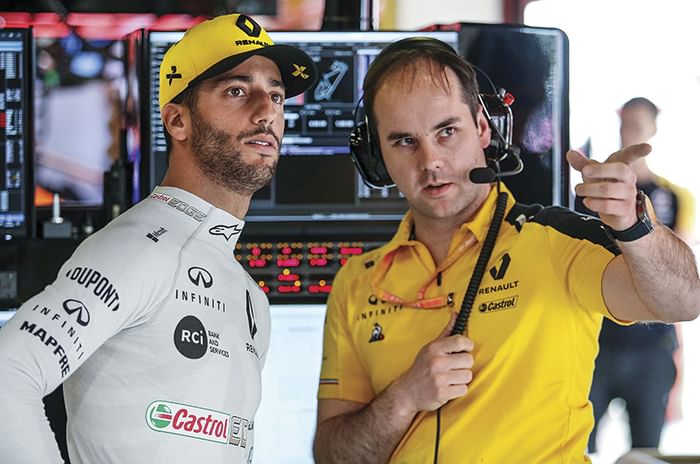
Ultimately, this is motor-racing and what makes the difference is speed. Most teams today log more or less the same quantity and quality of data, so there’s little competitive advantage to be had in data gathering.
Data analysis and processing is where the true battle for performance lies. The faster a team can process data, the faster it can apply the solutions it comes up with after having analysed it, the faster they will be on track.
“Anything where you can analyse things coming in as quickly as possible and find that good piece of data or the piece of data that’s erroneous then that’s probably where you will get a competitive advantage,” said Nathan Sykes, Chief Data Officer at the Renault F1 team. “When something doesn’t work as expected, you tend to find that the answer’s somewhere in the data. It just takes you days, weeks, months to find it. If you can turn that down to seconds or fractions of a second then your development will be significantly quicker.”
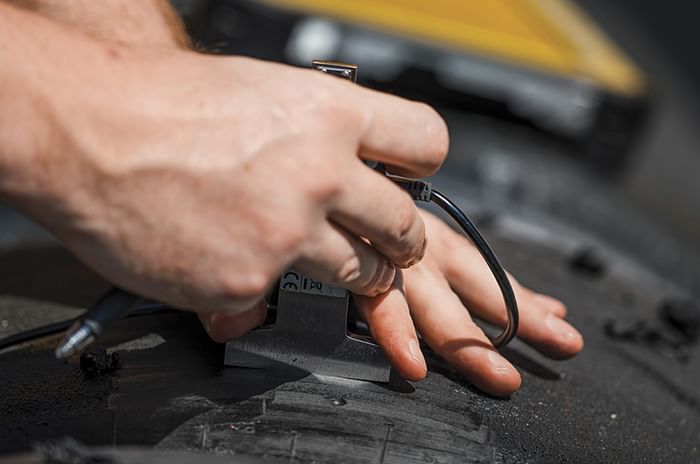
“Yes,” John McColgan adds. “There will be developments on the car, sensor technology is progressing all the time, sensors are becoming smaller so we can fit more and sensors are becoming more reliable. But, really, the big step we’re hoping for is that things that are being developed in terms of data, in terms of machine learning, they will accelerate our ability to understand and react to the data that we are gathering.”
Comments
Member Login
Personal Details
No comments yet. Be the first to comment.