Formula One is the pinnacle of motor racing and the cars that race here are the most technologically advanced racing machines on the planet. But perhaps no single element illustrates this point better – or pushes the technology envelope harder – than the Power Unit.
The Power Unit is the miracle of technological wizardry that sits at the heart of and powers a Formula One car. This turbo-hybrid powerplant replaced the naturally aspirated engines Formula One used until 2014.
Renault, instrumental in pushing the sport toward the shift, is one of just four manufacturers developing these incredible works of engineering art, supplying customers McLaren as well as their own works Renault F1 Team.
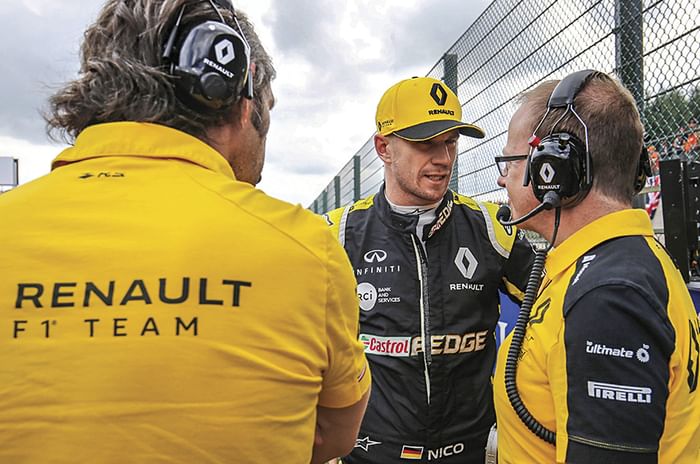
The cut and thrust of competition means that the Power Units they and their rivals have built are not only among the most efficient powerplants motorsport has ever seen, but possibly the most powerful engines in Formula One history.
“It’s the way to go,” says Pascal Tribotte, Renault F1 Team’s Technical Coordinator, who works out of the team’s engine facility in Viry-Châtillon and is the architect of the manufacturer’s Power Unit. “Formula One is the flagship of racing so it’s quite normal we have the more complex technology. It also brings valuable knowledge to Groupe Renault to see the limits of the technology in Formula One.”
NOT JUST AN ENGINE
‘Complex’ is certainly one way of describing the Power Units. They perform the same function as the engine; in that they power the car. However, the engine today is just one of six separate elements that make up the whole.
At the heart of the Power Unit sits the internal combustion engine – a V6 with a 1.6-litre capacity. It is fitted with a turbocharger and mated to two hybrid systems:
The MGU-K (Motor Generator Unit-Kinetic) system is an evolved version of the KERS system that Formula One introduced in 2009. It recovers kinetic energy under braking that can be stored in a battery and then used to power the car. The amount of electrical energy it can deliver to power the car is capped at 120kW.
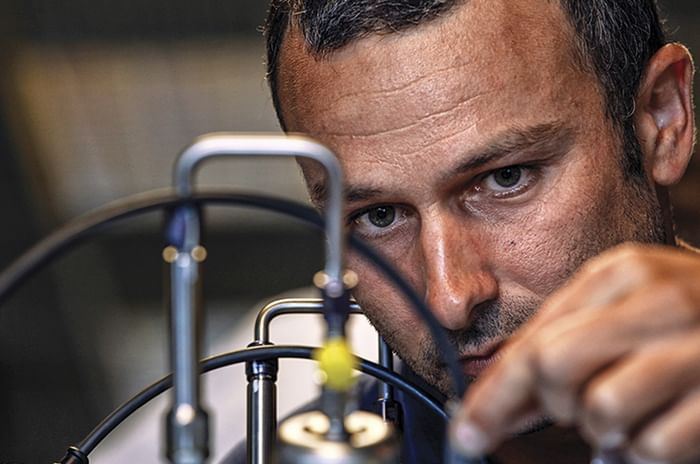
The MGU-H (Motor Generator Unit-Heat) recovers heat energy from exhaust gases that can either be used to send extra power to the rear wheels via the MGU-K or to spool up the turbocharger to cut out turbo-lag.
The battery is where harvested energy is stored, ready to be deployed, with the amount that can be deployed limited to 4MJ/lap.
Controlling all of this technical wizardry, the brain in charge of the harvesting-deployment interaction, is the Control Electronics.
At 1.6 litres and with six cylinders, the engine is far smaller than the 2.4-litre V8s Formula One previously used or the 3.0-litre V10s and screaming V12s that preceded them. But mated to the turbocharger and all the hybrid systems, the 1.6-litre can produce raw power in the region of an incredible 1,014hp.
The move to the turbo-hybrids in 2014 made the powerplant a significant performance differentiator again; after several years of engines whose performance was frozen by regulations.

Getting so many different elements all optimal and working together correctly can yield a huge advantage.
The number of Power Unit elements a team can use over a year are capped at three (and in some cases, two). Exceeding that allocation can trigger costly grid penalties. There are therefore limited opportunities to introduce performance upgrades.
Decisions taken during the design process of the Power Unit are therefore crucial. Here’s how Renault goes about it.
“For an engine manufacturer it always starts with the power target,” says Pascal Tribotte. “We know each season we have to win an amount of lap time through the engine and most of it will be power. So we define a power target. We estimate what our competitors will gain over a year and we try to do the same or more.”
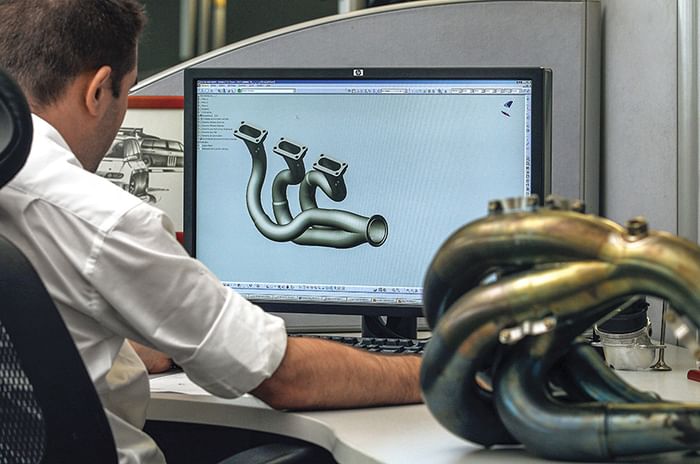
THERMAL EFFICIENCY
Pascal Tribotte and his team unlock the gains by boosting what is known as the Power Unit’s thermal efficiency. The amount of fuel flowing into the engine is capped, by regulations, at 100kg per hour.
Which means the only way to extract more power from the Power Unit is to make it more efficient. The equation is simple: the higher an engine’s thermal efficiency, the less the energy lost in the form of heat or sound.
The thermal efficiency of Renault’s Power Units is upwards of 50 percent, which means the team is harvesting or recouping more than half the energy (that would have otherwise gone to waste) and ploughing it back into powering the car.
Designing the Power Unit is just the first step. Renault engineers at Viry-Châtillon also have to figure out how best to run the engine. They need to program the Power Unit to harvest energy and deploy it at the right time.
The harvesting-deployment interaction works differently in qualifying when you want every ounce of power and energy stored up going towards powering the car on its flying lap. On Sundays, ◊ ∆ the performance has to be eked out over a full race distance.
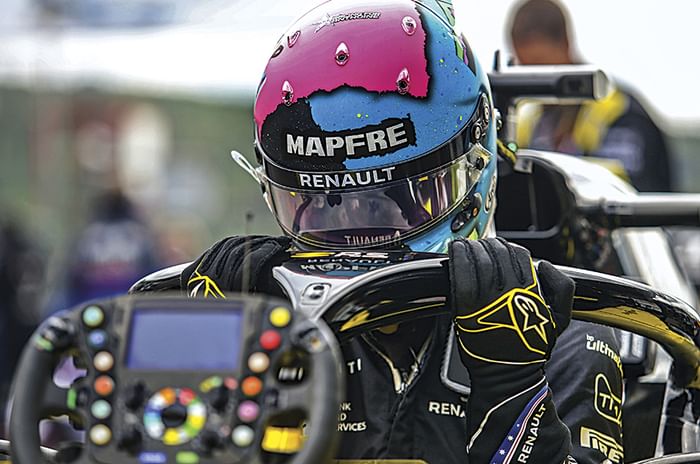
At high-speed Monza, for instance, which hosts the Italian Grand Prix, you want a kick of energy as you sweep out of the corners and onto the long straight. But you don’t want to be running out of electrical energy – known as clipping – in the middle of the straight, which would cost you crucial time in qualifying or make you a sitting duck for a rival in a race.
Renault relies heavily on software and simulation to figure out the most optimal harvesting and deployment relationship; but the learning curve in the first year was steep.
“It was very, very complex but also you have the right software developed, it becomes rather easy,” says Pascal Tribotte. “It was investment in programming and thinking what the best strategy to design a software for energy optimisation around a lap is.”
“We also have software in the car to refine the optimisation, depending on, for example, the race conditions; like if you want to recharge your battery because you’ve used too much of your MGU-K to overtake somebody. There is also a bit of software inside the car so the driver doesn’t have to care about energy optimisation. It’s quite automatic.”
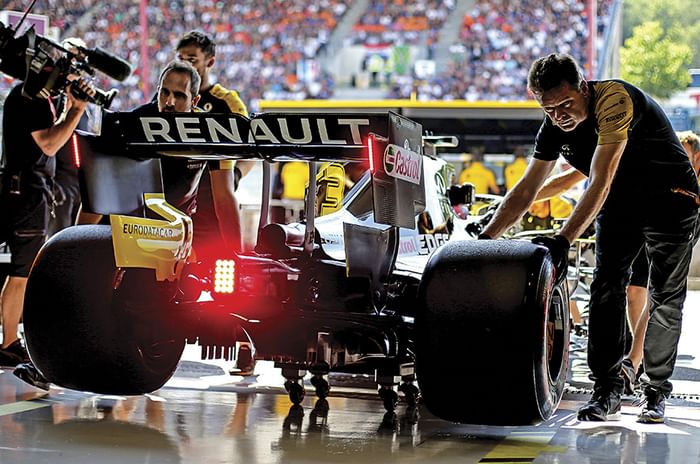
PERFECT FIT
As much of a performance differentiator the Power Unit has become, aerodynamics is still a
big determinant of who’s fast and who’s not.
Integrating the Power Unit into the chassis therefore is extremely crucial. No point designing the most powerful Power Unit if it’s going to be an ill fit in the car. At the end of the day, it’s about developing the fastest overall package – chassis and Power Unit combined – and not the most powerful Power Unit, nor the most nimble chassis.
A lot of the packaging requirements such as Power Unit dimensions, mounting points for the gearbox or suspension are prescribed by the rules.
But there areas teams can experiment with, such as the placement of the turbocharger or the design of the cooling systems, which if done right can yield hefty performance gains.
In this regard, as a manufacturer-backed squad, Renault F1 Team has an advantage even if it requires some co-ordination between its headquarters in Enstone and engine base in Viry-Châtillon.
“We have working groups on many fronts in terms of integration,” says Pierre Genon, the Head of Renault F1 Team’s Performance Systems Group. “That’s at the heart of what we do.
“We are a works team so we have an opportunity to focus on the whole package, not just half of it. The objective is always the fastest car. Some groups focus on performance, some will focus on reliability, some will focus on specific aspects of design like cooling or exhaust, which touch both sides and are probably more involved in the performance aspects, and then mechanical integration.”
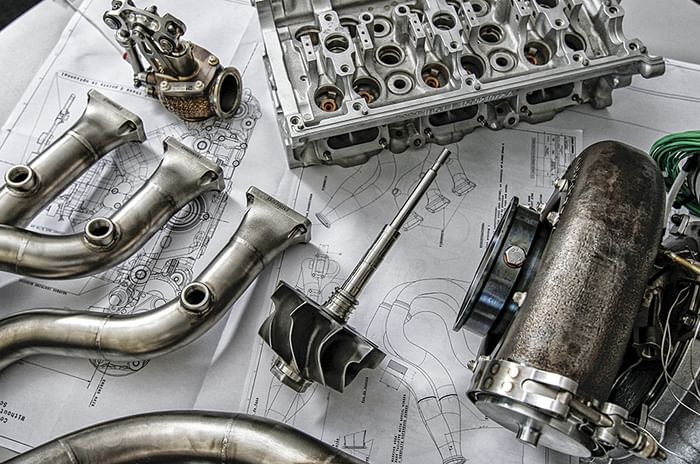
Work on the Power Unit begins some time before the chassis is designed. In order to avoid the chassis effectively being compromised as a result of having to be designed around the engine, communication between Enstone and Viry-Châtillon is crucial.
The conversations around Power Unit integration go beyond just the packaging. The new Power Units are integrated with a car like engines have never been before.
For example, the MGU-K has changed the scope of the rear brakes. It slows the car down to such a degree when it harvests kinetic energy that teams now run, minimal, skinny brake discs at the rear, essentially supplementing the braking power of the MGU-K.
That is why when it fails, it not only means a loss of power but also a loss of braking power.
“It was a little bit more straightforward with the V8,” says Matt Harman, Renault F1 Team’s Engineering Director. “Even when we had KERS it was a separate system from the main engine system, whereas now the system is very, very linked to the MGU-K and the MGU-H.
“So we have to be careful, and those conversations need to be very in-depth. We need to use an awful lot of simulation tools to make sure these discussions are based around total car performance and not the local optimum. We spend a lot of time on making sure that the engine is essentially fully optimised within our particular chassis.”

Given the complexity of modern day Power Units, it wouldn’t be a stretch to say Renault are working miracles every time a car powered by their engines drives around a track. At the same time, they are gaining crucial road-relevant expertise.
The only mass-market car manufacturer racing in Formula One with its own team, Renault’s participation at the pinnacle of motorsport gives them an edge and positions them as a carmaker
on the cutting edge of the technology envelope.
Click here for Renault India models, prices, reviews, images, videos and more
Comments
Member Login
Personal Details
No comments yet. Be the first to comment.