If speed could assume form, it’s a good bet it would take on the shape of a Formula One car. Aerodynamic, sleek, all grace and poise; Formula One cars look quick even when just standing still.
Exotic works of art, with their sweeps and flicks, wings and aero-appendages, it probably comes as no surprise that it takes exotic materials to bring them to life.
Aluminium? Too low-tech for modern-day F1. No, underneath their shiny licks of paint and sponsor stickers, Formula One cars are made from space-age carbon composites.
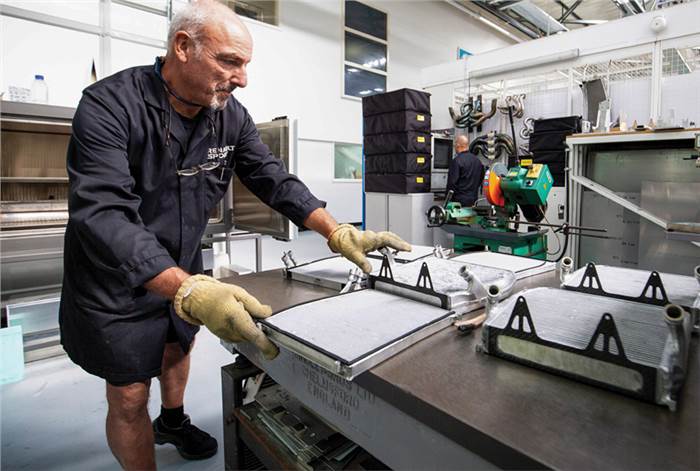
Lighter than aluminum and significantly stronger, making cars not just faster but also safer, carbon composites were first used in Formula One in 1981. The groundbreaking John Barnard-designed McLaren MP4/1 was the first F1 racer to be fully built from carbon fibre.
Barnard used the cutting-edge construction process for performance reasons, but the safety benefits of this new material were immediately proven when John Watson walked away unscathed from a heavy shunt in practice for the Italian Grand Prix at the fearsomely fast Monza.
Proving itself not just fast but also safe, Formula One was won over and today, every car on the grid – including the pair of Renault R.S.19s driven by Nico Hülkenberg and Daniel Ricciardo – is built from composite materials.
“By definition, composite materials are made from at least two constituents,” explains Jerome Lafarge, the Renault F1 Team’s head of materials.
“Carbon-fibre composites now make up almost 85 percent of the volume of a Formula One car whilst accounting for less than 25 percent of its mass.”
In certain areas of the car that may be subject to extreme temperatures and wear, a number of specialty composites are used, Jerome Lafarge says. These include carbon brakes, for instance, or carbon clutches.
“There are multiple possible combinations (of composite materials) depending on the constrains placed on a component,” he adds.
As quick as it may look standing still, a Formula One car isn’t built to look good in its garage, but instead to tear around a racetrack.
As it does so, different parts of it are subject to different forces, each placing its own unique demands on different areas of the car.
At the heart of it all sits the monocoque, an extremely strong but light structure where the driver sits and to which all other parts of the car are fitted. It is the strongest and safest part of a Formula One car.
“As a central element of the car, all of the other load bearing structures are directly attached to it,” says Jerome Lafarge.
“Forces are fed in through the front suspension as the car responds to circuit perturbations but also through the engine and gearbox rear suspension assembly.”
“Aerodynamic loads are fed via wings and G-forces from drivers.The car must resist all these various forces effectively if it is to contribute to the overall performance. It is necessary, therefore, to design sufficient stiffness into the chassis to minimise deflection under load.”
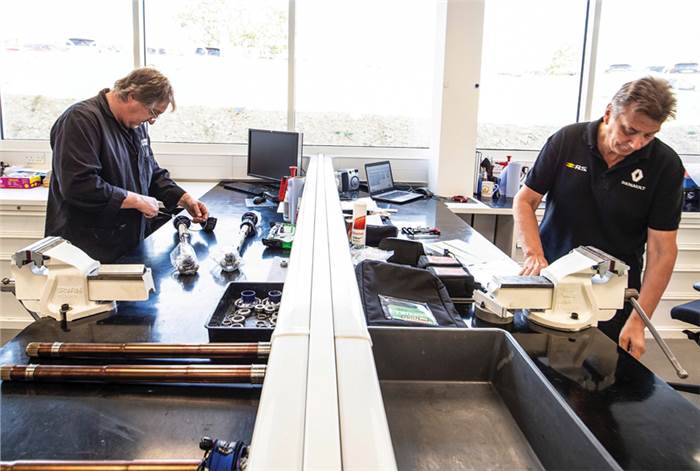
To cope with these different forces, different parts of the car, while still built from carbon-fibre composites, are constructed using varying processes.
Some parts have to be stiffer than others. The front wing, for example, has to be stiff enough not just to withstand the aerodynamic loads placed upon it but also so that it doesn’t deflect or bend more than the rules permit.
The gearbox, meanwhile, has the rear suspension mounted directly onto it. So, not only does it have to withstand the punishment it is put through every time Daniel Ricciardo and Nico Hülkenberg clatter over a kerb or kiss a barrier, it has to do it over six consecutive race weekends, as required by the rules.
So, components like the front wing, the crash structures and gearbox have to be reinforced more than other elements of the car that don’t go through as much punishment.
“Main benefits from composite materials are their high specific strength and stiffness per unit of weight compare to metals,” said Jerome Lafarge.
In addition to the obvious weight saving, composites have an almost infinite fatigue durability and so can be made far more cost effective than the metals parts they replaced.
“Furthermore, composite materials exhibit lower extensions to failure and are extremely anisotropic (exhibiting different properties when loads are applied in different directions).”
“This must be accounted for in any design calculation and (we) are only capable of specifying the performance under certain loading regimes.”
“Interface between matrix and reinforcement has a major influence on the properties of the composite.”
Reinforcement is added using materials like Kevlar to the composite, varying the ratio of the composites in relation to each other, or even using different kinds or resin. Suffice it to say that it’s a complex process.
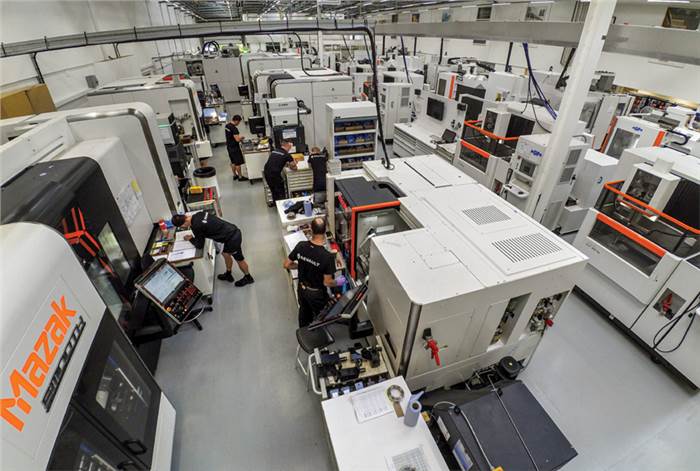
However, adding reinforcement adds weight, which takes away from performance, which is why construction is so specifically tailored. But where does all this magic happen? Back at the Renault F1 Team’s base in Enstone, England.
“We employ 145 people in the composite department,” says Keith Dunsby, head of composites at the Renault F1 Team.
“We have got many different skill profiles in the department. We’ve got laminators, trimmers, pattern makers, programmers and machinists.”
The process starts in the design office. Renault’s design team dreams up the fastest possible car within the limits of the regulations. Once the designs are signed off, it’s over to Keith Dunsby and his team to turn them into reality.
“When the designers have designed a component, before we make that we have to make a pattern and a mould.
“So, we have a programming team that will program by CAD the patterns to be machined. They will then be blocked-up by the pattern makers in the pattern shop using Epoxy Resin Block.”
“Then the process is to have those machined. We currently have got five 5-axis machines where we can machine patterns on.”
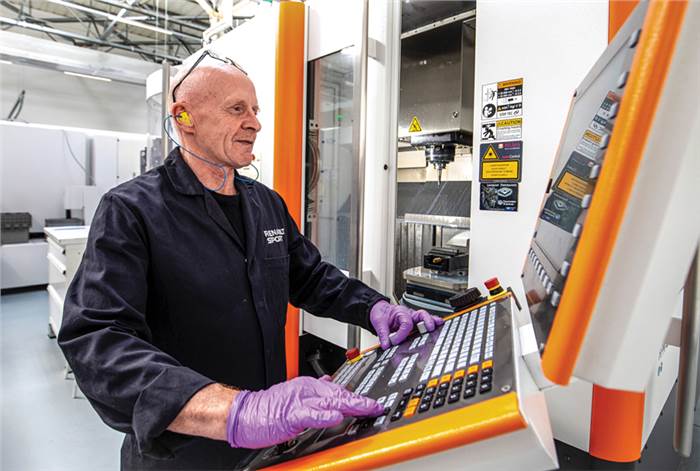
“We machine the patterns, they get inspected and then come back to the pattern shop where they’re prepped for making moulds.”
“The carbon-fibre moulds are made in a clean room where we have 75 laminators currently spread over three shifts, with room to expand.”
“In the clean room, the process is then to get the 6mm thick mould made and they go in to the autoclave and they are cured at pressure.”
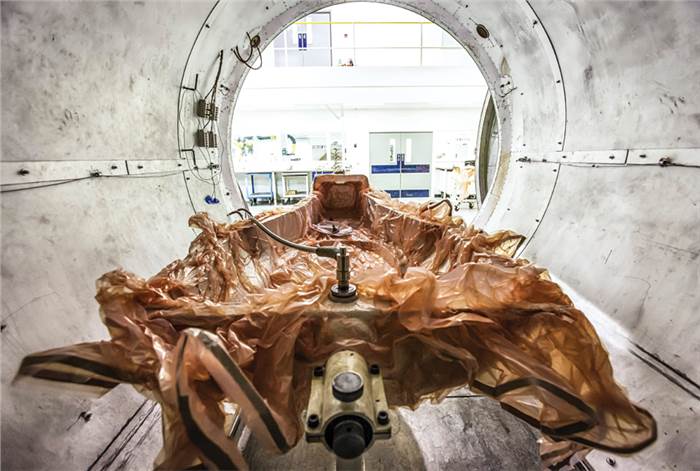
The components are cured at 135deg C and at a pressure of 100PSI. That’s the general rule of thumb but Keith Dunsby’s team works with a whole range of weaves and carbon composites that need to be cured differently.
Some components are solid carbon, some have an aluminum core, others have a material called Rohacell in them.
Regardless, they all must be cured; and only once that is finished are the parts for the car ready to be manufactured.
“We make a lot of different components in the cleanroom. We make all the suspension in house, all A-class components like the chassis, we make our own gearbox, carbon-fibre noses, front wing, oil and water pipes, pressurised tanks, bodywork and radiator ducts etc.”
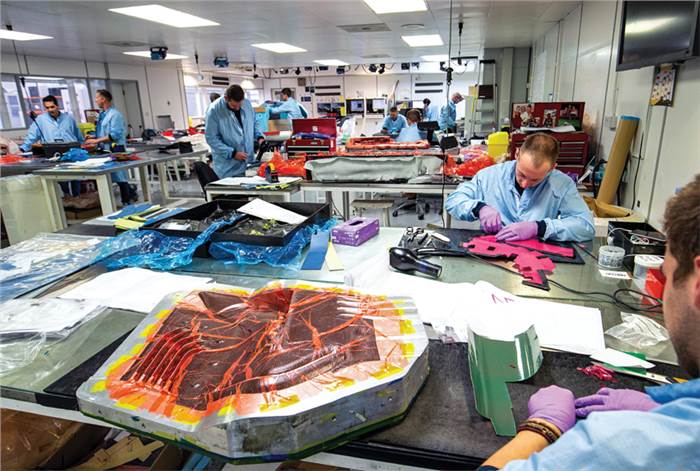
“We’ve got four autoclaves which are running 24/7. We make over 12,000 components during the season so it’s a big, big turnover of parts.”
It’s a complex, long drawn-out process. But in Formula One, speed is everything – that includes the speed with which you can bring new, upgraded parts to the car. Keith Dunsby and his team are, therefore, locked in a constant race to cut down lead times.
“We’ve been tasked this year with improving our lead times,” he says. “We actually did a front wing for the first time this season in six weeks.”
“A chassis typically will take five to six weeks to make at least. The whole process (putting the entire chassis together) is probably eight weeks to get it all completed.”
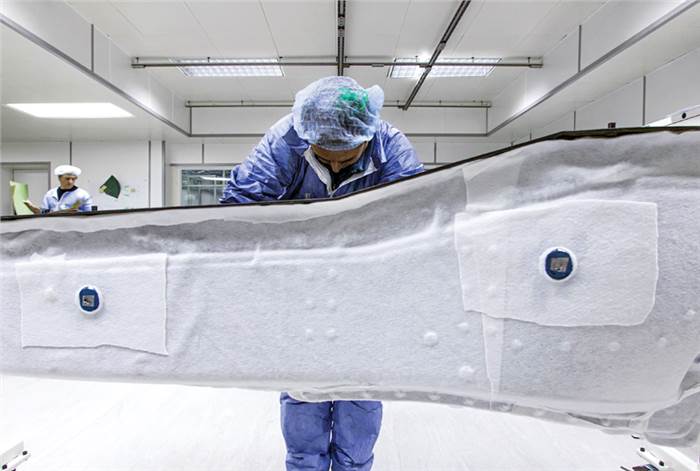
The composites department also must accommodate enough flexibility to build-up a supply of spares to cover for the inevitable accidents and crashes.
“We try to task ourselves with making one front wing a week,” adds Keith Dunsby.
“Rear wings, we tend to try and do at least two a week, they’re not quite so complicated as the front wing.
“Bargeboards is another one where we’re forever making a pair a week as well to keep up with the damage.
“A lot of the parts are in vulnerable positions. We try to keep one running set of parts in our stores so that we’ve got a set of parts back at the factory and we can try and cover any damage that may take place at each race.”
Formula One has used carbon composites since the 1980s and it remains very much a pioneer, with the broader aerospace and automotive industry only just beginning to embrace the technology in the construction of road cars and commercial planes.
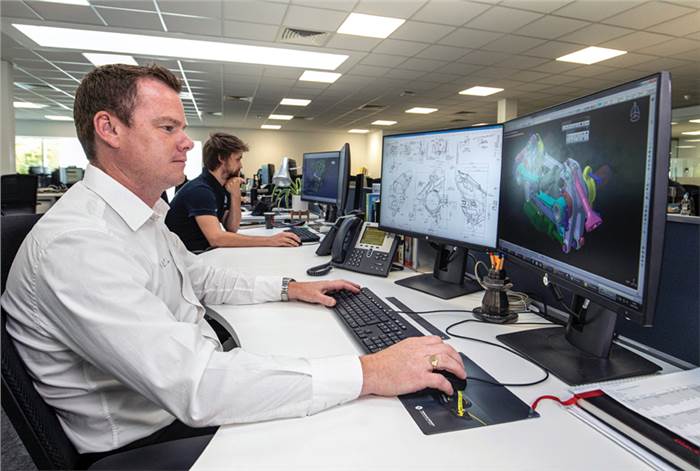
As a result, suppliers of composite materials and fibres use Formula One, with its constant search for performance, as a test bed to develop products for a wider commercial application.
“There is a lot of R&D work that goes on in Formula One regarding composites,” says Keith Dunsby.
“Most teams have got their own R&D composite facility and they’re always pushing their suppliers to get something lighter and stronger all the time.”
“Because we’re a smaller industry than the aircraft industry, we can do it on a smaller scale.
“The suppliers can do a smaller development with us and then it could be rolled out later to the bigger aircraft industry.”
As ever, even when it comes to composites, Formula One remains at the very cutting edge.
Comments
Member Login
Personal Details
No comments yet. Be the first to comment.