Tata Sanand plant tour: How the Nexon is born
We spent a day at the Sanand facility, which Tata has acquired and retooled for over Rs 2,000 crore to manufacture the Nexon and Nexon EV.
Published On May 23, 2024 02:00:00 PM
24,900 Views
Follow us on
About twelve months and a Rs 1,300 crore retooling exercise. That’s what it took Tata Motors to get its Sanand unit up and running after acquiring it from Ford for Rs 725.7 crore on January 10 last year.
It started rolling out petrol and diesel versions of its Nexon compact SUV in January 2024, and the same production line started making the Nexon EV in April. Moreover, it takes just 16 hours to manufacture a Nexon, claims the homegrown automaker. That’s because Tata added over 100 more robots to the Ford hardware and integrated JLR’s software and control units into the facility.
Spread across 460 acres, the factory has an annual production capacity of 3 lakh units, which, according to Tata, can be scaled up to 4.2 lakh units.
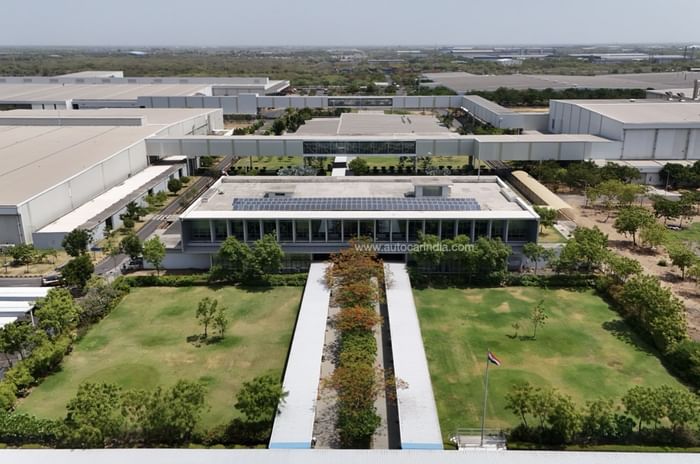
Despite the 44-degree Celsius heat, I was excited to get a peek inside what is said to be a state-of-the-art manufacturing facility. The tour began with the paint shop, though that’s not where the production process starts.
It was fascinating to see the Nexon’s entire monocoque being dipped into a vat of grey solution – this electro-static finish is what goes under the primer. Only after that are the primer and paint sprayed on by robotic arms, outside and inside. The company claims the Tata Passenger Electric Mobility Plant at Sanand, Gujarat, is among the first in India to have a continuously moving paint shop line, which has a 50 percent automation level. Factory workers take up the final polishing work.
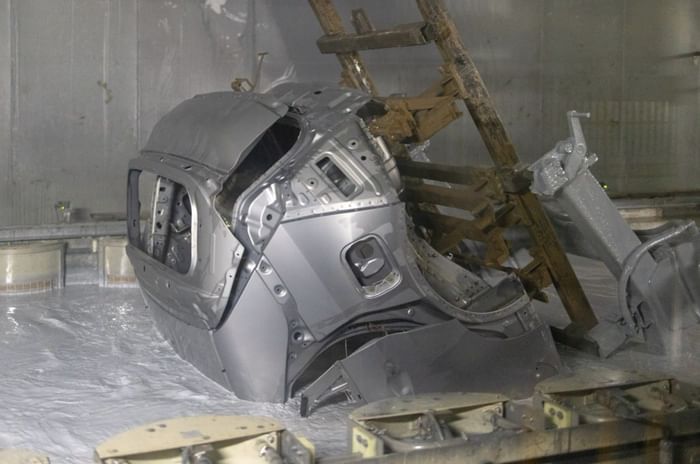
But before that, the vehicle’s underbody is mated to the doors through automated spot welding machines. What’s somewhat unique is that none of these large body panels are manually forklifted; instead, automated lifts and robotised arms are used. Later, the roof is installed in a separate section. The weld shop is said to be 98 percent automated (specifically for spot welding), and the automation level in the press shop is 80 percent, claims the company.
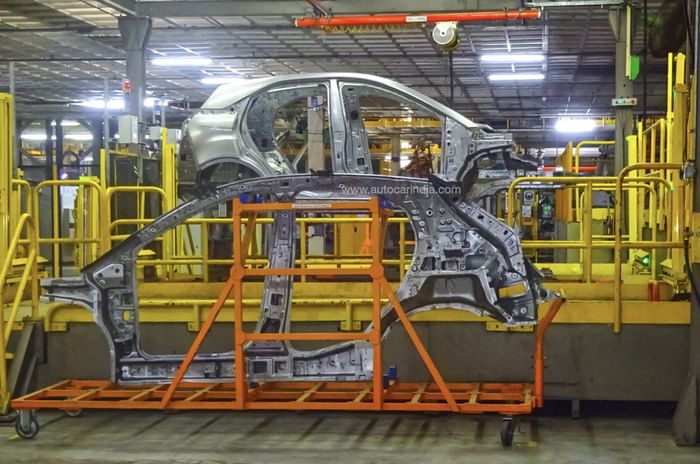
Once finished in its final colour (sans the polish), the Nexon is ferried to the powertrain line, where the ICE (including CNG) and the EV powertrains, along with other mechanical systems, such as the suspensions and brakes, are bonded to the chassis.
Tata Motors has confirmed that the production line is modular. So, it can produce four different platforms and up to eight variants simultaneously without sorting the models into batches. This gives the brand the capability to produce its upcoming Curvv, among other models, at the Sanand plant at the same time as the Nexon.
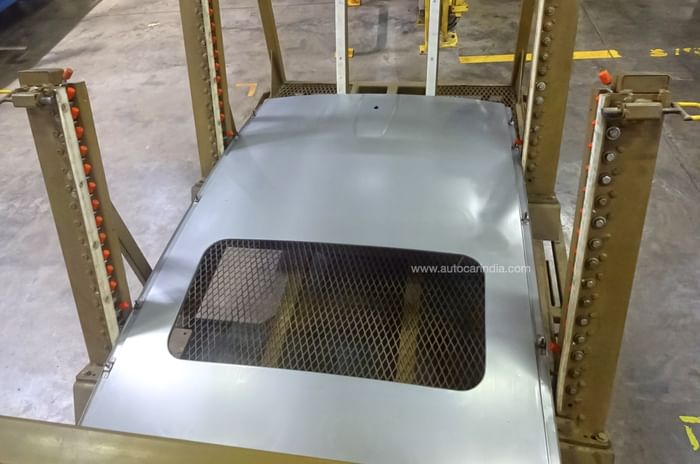
As the compact SUV rolls off the production line’s end—the TCF (Trim, Chassis and Final) shop—where, as the name implies, all the variant-specific features and trimmings are added, the engine (or electric powertrain) is started for the first time.
The Nexon then slides off the conveyor belt on its own and heads for inspection, which was quite exciting to watch. It undergoes another systems check for functions like the 360-degree camera. Finally, the SUV is taken to the in-house test track to ensure it meets Tata Motors’ standards for ride and handling.
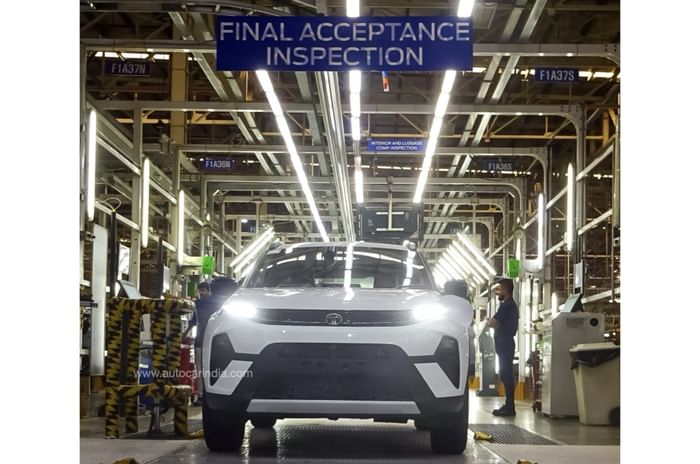
The Sanand facility employs over 1,000 workers, and most of them are former Ford employees. The automaker has even tied up with Ganpat University to upskill its workers at an in-house facility called Nalanda. It offers all its workers the opportunity to pursue UGC-approved diplomas, BTech and MTech programmes. It’s heartening to see that the brand is not just investing in automation and efficiency but also human capital.
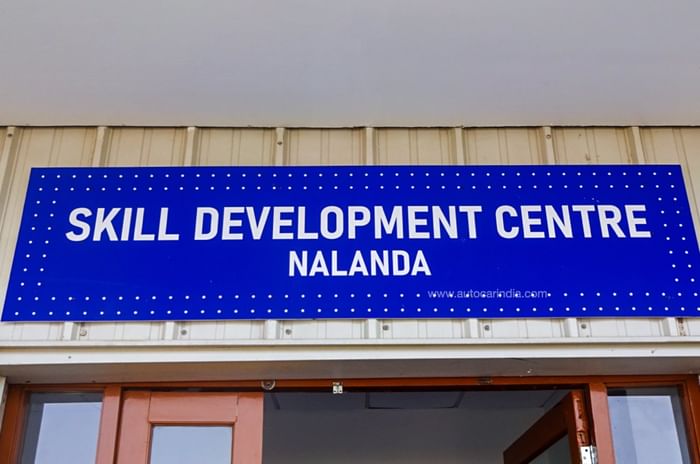
Also see:
Tata Punch EV road test, review
Tata Nexon likely to get panoramic sunroof
Tata Altroz Racer to get unique dual-tone paint scheme
Copyright (c) Autocar India. All rights reserved.
Comments
Member Login
Personal Details
No comments yet. Be the first to comment.