Getting factory fit, the Toyota way
Champions aren’t born; they are made. And proving the adage right is Toyota’s Technical Training Institute.
Published On Mar 16, 2025 08:00:00 AM
9,684 Views
Follow us on
It all starts with a simple ‘good morning’, but the hundred or so people gathered there are greeting no one in particular. They’re screaming this out at the top of their lungs, like a war cry. If you just teleported into their midst, you’d think this was an army battalion, but this is no fighting force at all. Welcome to Toyota Technical Training Institute’s (TTTI) morning assembly.
The assembly is like most others, with limbering-up exercises, presentations by students, and felicitations, if any, and then there’s ‘hello’, ‘thank you’, and other words screamed out again. Eighty-four decibels is what I measured on my phone’s app. “Shouting out aloud – hearing your voice clearly – helps rid you of your shyness, and we want all our employees, no matter their personality type, to be open and forthright,” says G Shankara, executive vice president for Finance and Administration at Toyota Kirloskar Motor.
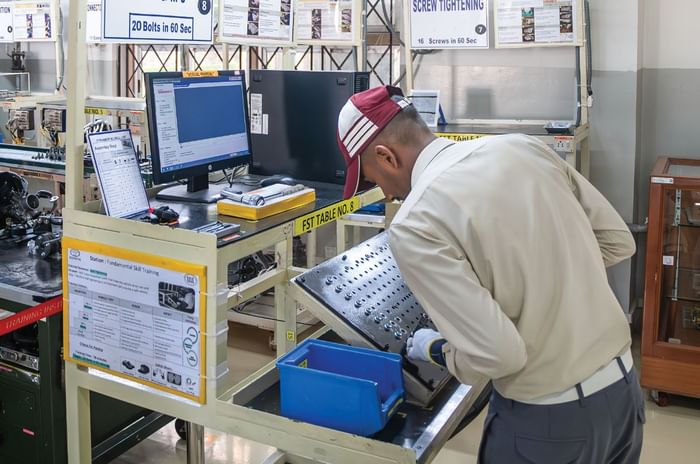
At a Toyota plant, that’s a key trait. Assembly line workers are encouraged to highlight mistakes so that others can learn. There’s even the famed ‘Andon cord’ that an employee can pull to get the help of a supervisor or even stop the line if the problem isn’t resolved within a preset timeframe. Supervisors never admonish team members and, instead, thank them for highlighting a problem and not simply sweeping it under the carpet or trying to rectify it hastily. It’s a cultural thing, says Shankara, that cannot be taught overnight.
Creating this culture is key for Toyota, and the curriculum and structure highlight this, with as much as a 50 percent focus on body and attitude, 34 percent on skill, and 16 percent on knowledge. This attitude is also visible in the facilities all around the campus; from classrooms, quadrangles, gardens, corridors and rooms, everything is maintained to a neat and exacting standard by the students. On a tour of the sleeping rooms, instead of unkempt beddings and strewn-about clothes typical of a youth camp, you find neatly kept beds and folded clothes, much like an army camp.
.jpg?w=700&c=0)
It’s clear to see that the institute looks well beyond just education. Established in 2007 at the company’s Bengaluru plant, it offers a three-year residential training programme covering four streams: Automobile Assembly, Automobile Weld, Automobile Paint and Mechatronics.
The courses are similar to an Industrial Training Institute (ITI) programme and are recognised as a National Apprenticeship Certificate (NAC) by the National Council for Vocational Education and Training (NCVET). All TTTI students get employed in the Toyota network and are free to seek a job outside it, but virtually no one does, says Shankara. It’s not hard to see why.
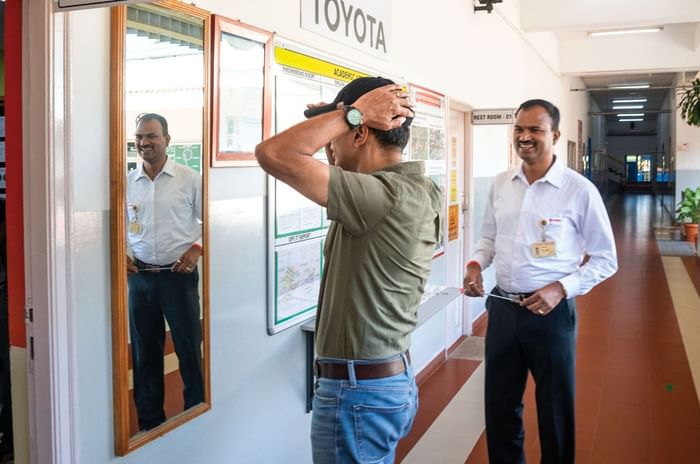
The youth are handpicked after an initial assessment and, interestingly, for an industry that has traditionally employed male workers, Toyota says that of the current 1,200 students, 600 are women. Students are typically from underprivileged backgrounds, and the entire programme is free of cost. And it’s not just education; the company also covers boarding, uniforms and food. While this may sound like a CSR-driven exercise, Shankara quickly points out that the entire programme’s expense is outside of Toyota’s CSR budget.
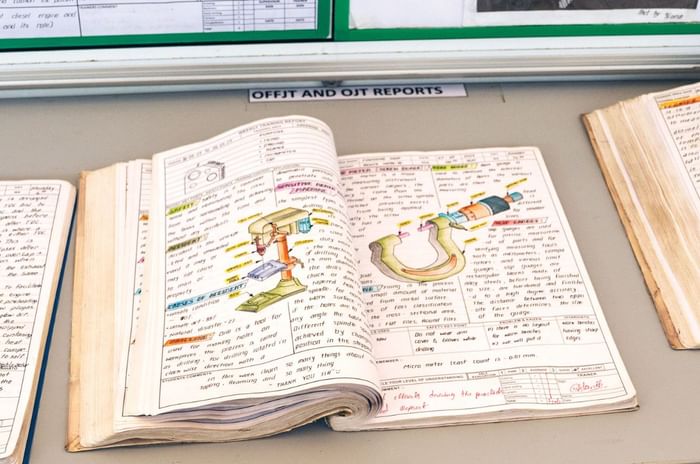
Fine arts
It makes its own business case, as Toyota gets a steady stream of manpower – well- trained and ingrained into the Toyota way. This Toyota way is so cherished that those selected for employment from outside the institute are trained at the company’s ‘Gurukul’ finishing school in three levels: Fundamental Skill, Element Work and Standardised Work training. The Gurukul facility also provides skill training for the dealer and supplier staff. Toyota India is also proud of the fact that it has so far produced 221 medal winners at Toyota’s global skill contest.
.jpg?w=700&c=0)
At TTTI and Gurukul, a lot of time is spent developing fine motor skills, making them second nature. Craftsmanship is what the end game is all about, and a lot of time is spent playing games that develop students’ dexterity. Beyond skills, there’s also a lot of safety awareness drilled into them, right from demonstrations of how you could easily lose an appendage – with props, of course – to the use of personal protective gear.
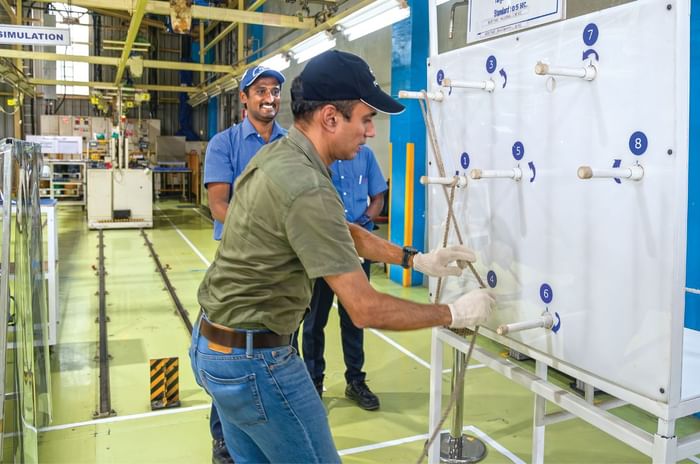
At every walking intersection, whether it’s the factory floor or the canteen, all employees must stop and look all three ways. And they do it; some more quickly or less fastidiously than others, but they all do exactly that. It’s clear that, at Toyota, you are moulded into the Toyota culture, and you could argue that this would stifle creativity and individuality. And while it does so to some extent, it’s also what the nature of the job requires. Besides, employees are encouraged to share creative ideas to make jobs easier, safer or more cost-efficient. The company says employee suggestions save a lot of money, and every year, multiple changes are implemented into the work system. Continuous improvement is a working mantra here.
.jpg?w=700&c=0)
Floor test
After the institute tour, we head off to the factory floor to see all this in operation. What is very apparent is the high percentage of a human workforce. These days, many factory floors are thinly staffed, some even resembling an eerie post- apocalyptic scenario, with machines humming away and not a single person in sight. Here, however, it’s a beehive of human activity. There is some automation for sure, but just not as much as I’ve seen elsewhere. Handcrafted isn’t just a term bandied about by the marketing folks; it’s very much in practice here.
.jpg?w=700&c=0)
As we move along, the ‘Andon cord’ is pulled at the trim line; some problem with the dashboard. What strikes me is the notification: there are flashing lights but no blaring alarm; instead, a soothing musical jingle is played out to get the supervisor’s attention. Whatever the problem, it gets sorted out; the line isn’t stopped, and the operation just keeps humming, much like the Toyotas being built here.
Games people play
Clockwise: Japanese Kendama toy to improve hand-eye coordination; Identifying fluids by smell; Finger placement, hand angle and pressure are key to detecting surface flaws; Trying to decipher nuts from bolts by just the sound.
Games are intrinsic to the training to hone hand-eye coordination, motor skills and all five senses. Yes, even smell. For instance, line employees can distinguish between different oils and lubes purely based on their smell, having practised with beakers filled with these fluids. The liquids vary in colour and are stored in different types of containers, but error-proofing means that if things get mixed up, an operator would be alerted by just the smell of it. There’s a fairground wire game where you have to pass a small loop over a twisted charged wire without touching it and setting off an alarm. The Japanese Kendama toy is also used; students spend hours tossing the wooden ball and catching it on the spindle. More specific to operations is the bolt- tightening exercise, which I try out. I have to reach into a bucket and pick up exactly five screws with one hand, then roll each forward to my thumb and index finger and tighten them with a powered screwdriver – sounds simple, but just picking up exactly five is a challenge, and then rolling each forward, I proceed to drop some. Needless to say, students do this again and again until it’s like a flawless machine rhythm.
.jpg?w=700&c=0)
Also see:
Generation Speed 2025: Motoring Disneyland
Slideshow: The day Narain Karthikeyan made his F1 debut
Copyright (c) Autocar India. All rights reserved.
Comments
Member Login
Personal Details
No comments yet. Be the first to comment.