Behind the scenes at Tata Motors' crash test facility
We take you through all the internal procedures that Tata cars, SUVs go through in order to ensure a high safety rating.
Published On Mar 01, 2024 08:00:00 AM
20,624 Views
Follow us on
If there’s one carmaker who has spurred interest around vehicle safety in recent years more than anyone else, it would be Tata Motors. With as many as 5 vehicles with a 5-star safety rating from GNCAP and a minimum of 4 stars for its remaining lineup, Tata Motors has really put safety in the forefront for its vehicles.
The company recently took us on a guided tour of its crash test facility at its plant in Pimpri-Chinchwad in Pune, which is built to world-class standards, and is arguably one of the best in the country currently. The brand gave us a behind-the-scenes look at how the company conducts crash tests internally, and how safety aspects are incorporated right from the development stage of a vehicle. Let’s dive deeper in.
It starts at individual component level
It all begins at what Tata calls the Servo Acceleration Sled facility – think of it as a miniature crash test area where individual components are calibrated for safety, focusing specially on interior trims, features and safety systems. This is where the sensitivity of airbag systems, and their deployment, is tested, as well as components such as seatbelt pretensioners, dashboard trim materials, seats, steering wheel, and every other single aspect of the car’s interior.
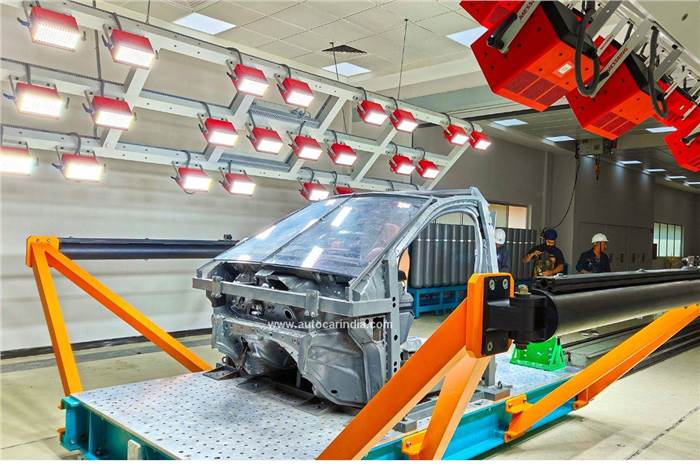
For instance, it can conduct tests to see how a dummy is likely to interact with the touchscreen in the event of crash, and fine tune its positioning if needed, or if the dashboard materials used pose a risk of scratches or deeper injuries, and likewise opt for the right materials. All of this happens right at the development stage, first as computer simulations, and then in full-size scale exactly as they would be put in the car.
The system comprises a rig on which a buck is mounted – the buck is a body-in-white structure either in full or in part consisting of just the front or rear frames, and comes fully fitted with the interior. The rig can be accelerated on a rail to speeds of up to 100kph before impact, generating over 30Gs of force, after which, the dummies in the buck are studied for the forces experienced by them, and how each interior element has interacted with the occupants.
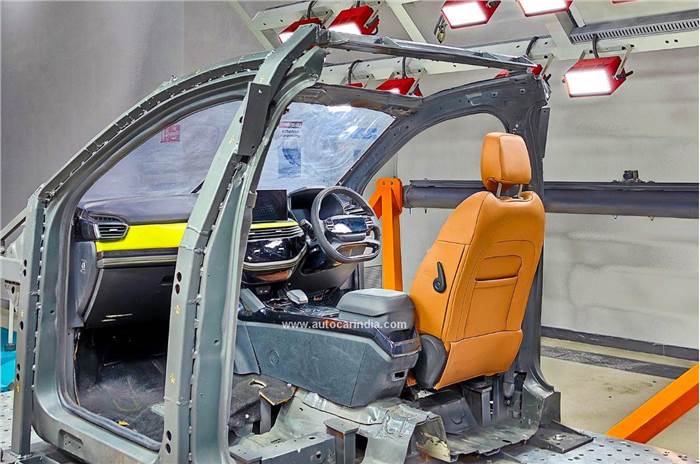
This is also a more cost and time effective way of carrying out tests to ensure that all systems behave as intended in the final full vehicle crash test. Conducting a full-fledged crash test is pretty expensive and usually takes 3-4 days in preparation. The Servo Sled tests, meanwhile, can be conducted more frequently, and its also a lot cheaper to calibrate materials and components at this stage before they are put in the car for final testing.
More than just ‘dummies’
The dummies are arguably the most critical aspect of the crash test, and they are really expensive. A single dummy can cost something between Rs 2.5 crore-3 crore, and Tata Motors has an entire family of them. These dummies – designed to replicate form, weight and articulation of a variety of body types – are fitted with as many as 42 sensors throughout their body, with each sensor sensing the impact on key areas, such as the knees, shin, pelvis, chest, neck and head. Even the rubber that makes up the surfaces of these dummies is meant to replicate human skin, which can experience a similar level of abrasion in the event of an impact.
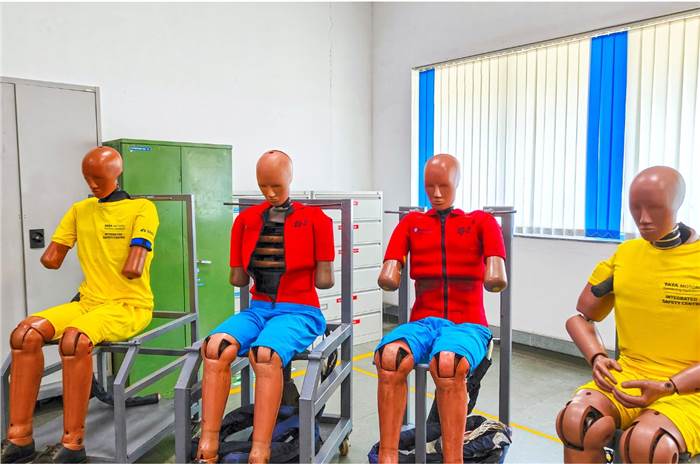
These sensors feed their readings into a data logger fitted inside the dummy, and after a crash test has been conducted, the data is downloaded by engineers and every parameter is studied to understand how the body was impacted. The dummies are regularly refurbished with new parts and sensors if there’s any damage sustained in a crash to ensure that they are always performing optimally. Even when there’s no visible damage, Tata Motors would still conduct calibration tests for individual body parts after a cycle of 5 crashes to ensure they are adhering to set parameters.
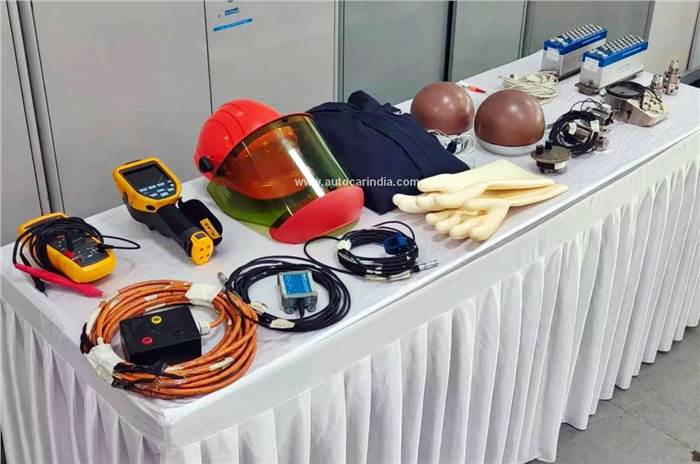
When not undergoing crash tests, the dummies are rather well-cared for – they are kept in a regulated environment with temperatures between 18-22 degrees and humidity of around 50 percent. These are international standards, which every test lab must adhere to so that a repeatability of the results can be ensured any where across the world. The company calls it ‘soaking the dummies’ before a crash test is to be conducted.

There’s also a separate set of dummies for ADAS testing. These, however, are not fitted with any sensors, but are draped in a resin material that’s meant to have the same reflective properties as human skin against radar or Lidar rays.
Spot of final action
After individual components and sub-systems are tested in the Servo Sled and the dummies have been ‘soaked’, it’s all put together for the final phase of testing. Tata’s crash test facility is really state-of-the-art, and not only conducts crash tests for passenger vehicles, but even for their commercial trucks and buses.
There’s a 200-metre-long tunnel that leads up to the actual crash zone, where there’s a huge concrete block, one side of which has a metal face replicating a wall. The crash zone is lit up with very high intensity lights that mimic natural sunlight, giving engineers the clearest possible view of the crash. There are at least 10 high-speed cameras outside the car, placed in every direction, and 5 inside, that record the crash at 1,000 frames per second.
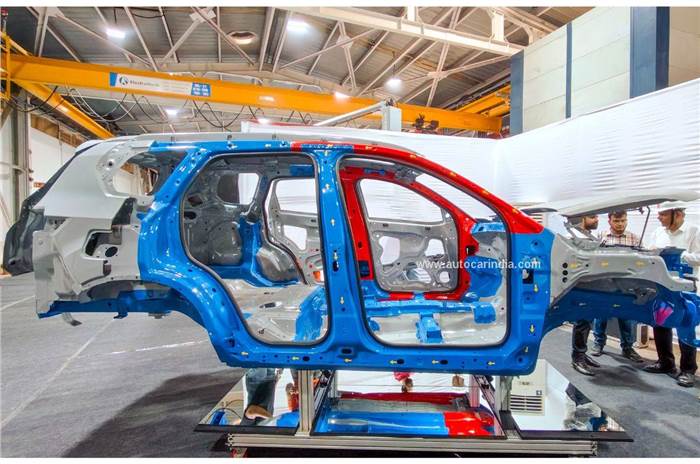
The crash zone can be adapted into conducting several different scenarios – offset frontal impact, head-on frontal impact, side impact, as well as side-pole impact. In the 40 percent frontal offset crash test that we were witness to, a brand-new Tata Safari was accelerated to a speed of 64kph through the tunnel using a system of pulleys, and bang – it was all over in a fraction of second!
A loud noise echoed through the hall as the Safari landed on its wheels, but from the looks of it, the body shell looked intact, and so did the dummies inside. Everything was as it was intended to be. But that’s something that only the engineers can testify, after they have analysed the exterior crash structures, the interior, as well as the data collected by the dummies. The damaged vehicle will be taken from the crash zone to a separate lab for analysis, after which it will be scrapped completely.
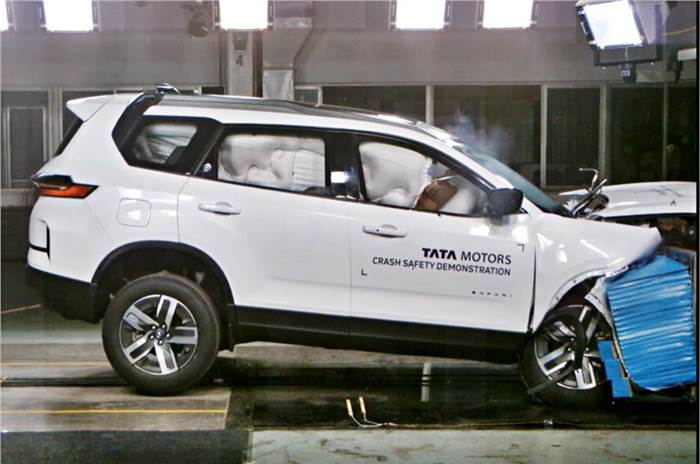
A lot goes behind engineering a 5-star rated vehicle, and seeing all the test procedures and the facilities first hand was an insight like no other. Tata Motors has invested heavily in keeping this sprawling facility up-to-date; it was established way back in 1997, and the results are there for us to see in their vehicles. But while manufacturers have made great strides in improving vehicle safety and delivering the right products, the onus also lies on us as road users to behave responsibly with our vehicles on our roads. A 5-star rated vehicle will keep you safe in a crash, but not from stupidity – education and awareness are most important here. So, stay alert and drive safe!
Also see:
Maruti Suzuki factory visit: Making of a Jimny
BMW 7 Series Protection: a close look
Copyright (c) Autocar India. All rights reserved.
Comments
Member Login
Personal Details
No comments yet. Be the first to comment.